In the dynamic world of logistics, crate handling plays a fundamental role in the safe and effective movement of goods. Whether it’s produce, electronics, industrial parts, or retail stock, crates are the preferred solution for controlled, stackable, and trackable shipping. One critical process that directly impacts the effectiveness of crate management is restacking. As more U.S. companies strive for leaner, more agile supply chains, crate restacking is fast becoming a pillar of operational efficiency.
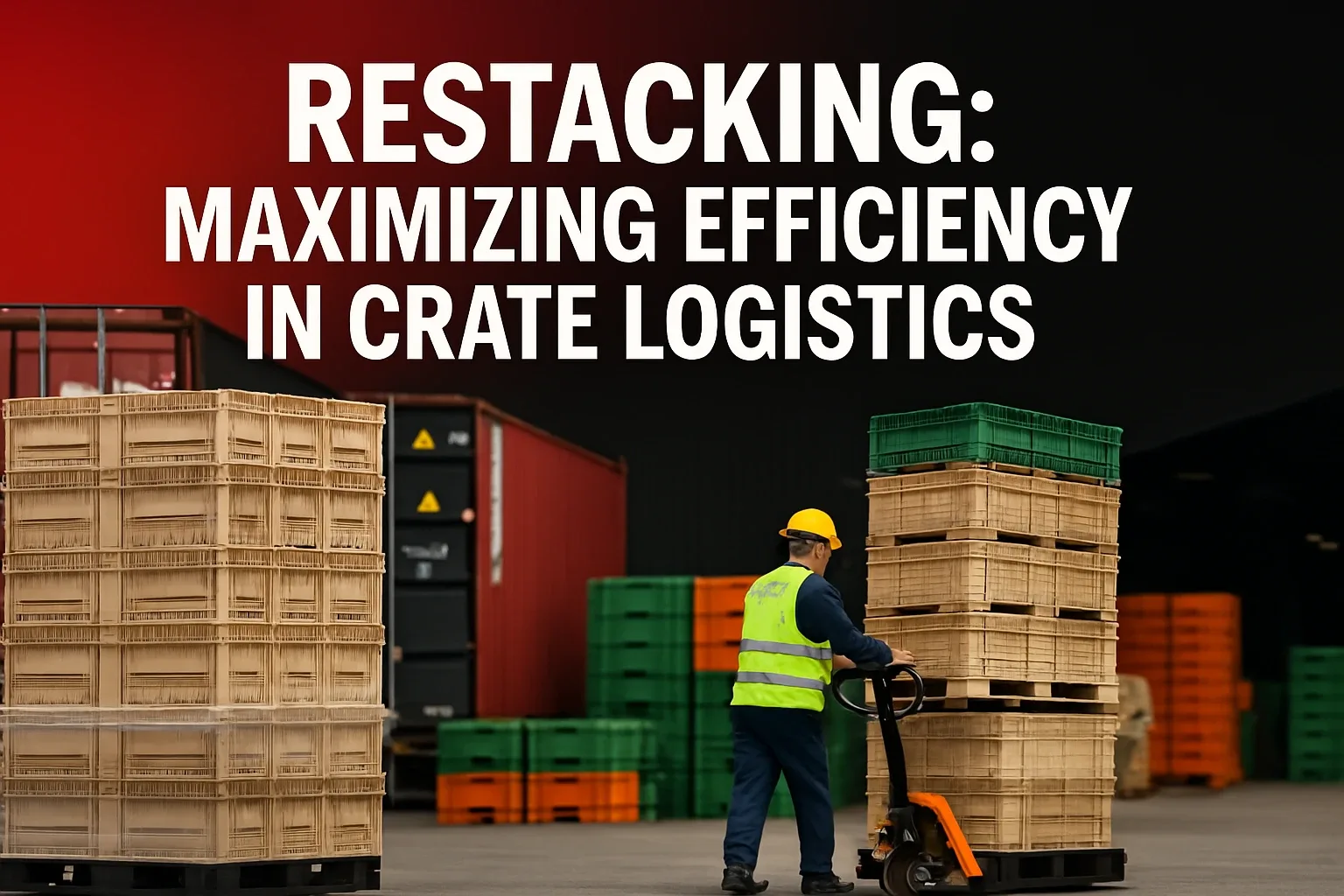
Restacking refers to the manual or automated reorganization of goods within or atop crates to optimize them for storage, handling, or transportation. Across America’s sprawling logistics network, crate restacking ensures goods are transported securely, space is used optimally, and damage is minimized during high-speed transfers.
Crate logistics are especially prevalent in industries where product integrity is non-negotiable—such as agriculture, food processing, automotive, and high-tech manufacturing. In these fast-moving sectors, poor restacking can mean increased waste, regulatory violations, and delays.
Why Crate Restacking Matters in the U.S. Logistics Network
The U.S. is home to one of the largest and most complex logistics infrastructures in the world. This scale creates tremendous pressure on warehouses, fulfillment centers, and carriers to deliver with speed, accuracy, and compliance. In this environment, restacking becomes more than a support function—it becomes essential.
Crate restacking supports American logistics by:
-
Enhancing crate stability for better stacking during transit
-
Ensuring even weight distribution for safer forklift handling
-
Facilitating accurate inventory checks and scan-based sorting
-
Making room for mixed-SKU or temperature-sensitive items
-
Reducing breakage rates and rejected deliveries
Because crates are often reusable and part of reverse logistics loops, correct restacking also prolongs their lifespan and minimizes asset damage.
Industries That Rely on Efficient Crate Restacking
Crate restacking is not a one-size-fits-all process. It adapts based on industry, cargo type, and end-customer requirements. In the U.S., the most active users include:
-
Fresh produce distributors who must meet USDA inspection protocols
-
Electronics brands shipping parts that require impact-proof stacking
-
Automotive suppliers managing inbound parts from multiple locations
-
Foodservice and grocery warehouses managing fragile or chilled items
Each of these industries uses restacking to reduce handling errors, avoid compliance risks, and keep goods moving through complex logistics pipelines.
How Crate Restacking Supports Warehouse Efficiency
Warehouse operations are under immense pressure to turn inventory faster and manage more SKUs in less space. Restacking in crate operations can dramatically improve:
-
Shelf and bin alignment for automated picking systems
-
Repackaging accuracy when creating store-ready units
-
Zoning compliance for refrigerated and frozen products
-
Faster load-unload times during peak receiving hours
By reducing unnecessary handling and organizing crate content by priority or batch, restacking helps warehouses hit daily throughput targets more consistently.
Manual vs. Automated Restacking in Crate Handling
Many U.S. warehouses rely on manual labor for crate restacking, especially when dealing with fragile or mixed goods. However, automation is growing.
Advanced facilities now use robotics and conveyor-integrated crate stackers that:
-
Detect crate height and shape variations in real time
-
Balance weight distribution using onboard sensors
-
Adapt stacking based on destination, temperature zones, or truck routes
These systems reduce human error and increase speed, allowing for 24/7 operation with reduced risk of injury.
Crate Restacking as a Sustainability Driver
One overlooked benefit of restacking is sustainability. With crates often made of plastic or heavy-duty composite materials, minimizing wear through proper restacking means fewer replacements.
Additionally, efficient stacking:
-
Reduces wasted truck space, lowering emissions per shipment
-
Encourages crate reuse within closed-loop distribution models
-
Cuts down on filler materials like bubble wrap or foam
This aligns crate restacking with broader ESG (Environmental, Social, and Governance) initiatives in American logistics.
Implementing Crate Restacking in Your U.S. Operations
For companies looking to improve crate handling, implementing a restacking solution involves:
-
Auditing current stacking patterns and crate damage history
-
Training staff in safe and efficient restacking methods
-
Investing in crate-compatible stacking machinery or software
-
Creating SOPs based on product type, weight, and temperature needs
It also includes data collection—knowing how restacking impacts delivery quality, labor hours, and freight costs is critical to long-term ROI.
The Future of Crate Logistics and Restacking in America
The restacking process is no longer a simple side task. For U.S. companies managing high volumes of crated goods, it’s a core function that ties directly to profitability, compliance, and customer satisfaction.
As technology becomes more accessible, expect to see restacking integrated directly into warehouse execution systems, combined with AI for real-time optimization.
Whether you’re distributing avocados, brake calipers, or network switches, restacking ensures those crates arrive safely, consistently, and efficiently.
The role of restacking in crate logistics across the USA will only grow more critical—and companies that master this process today will lead tomorrow’s supply chains.